Brush Beam Improves Prototyping with 3D Printing
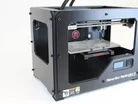
The explosive success of 3D printing is finding applications in a new area for prototyping and manufacturing: dentistry. Beam Brush, whose main claim-to-fame includes the recent release of the first blue chip-embedded toothbrush to track healthy brushing habits, is effectively shaking up the medical device supply chain while netting huge savings.
“We wanted to build a stand for our toothbrush because early customers had started asking for one,” Beam Brush cofounder Alex Fromeyer said in an interview. An innovative answer came in the form of 3D printing. Now, he said, “we are one of the first consumer medical device companies to use 3D printers and one of the first companies to own the Replicator 2.”
Beam Brush, the World’s First Smart Toothbrush
This move allows the digital health startup a huge amount of flexibility and independence from start to finish.
“We didn’t have to engage the mold maker at a cost to us because we were 90% of the way there,” said Fromeyer, explaining the mold maker simply transferred the spec from the MakerBot format to its software after the initial design had been finalized in-house. “We also built our own supply chain and we do packaging and fulfillment.”
Beam Brush has now extended the process to make manufacturing and assembling brushes more efficient.
The company, currently partnering with Delta Dental and Humana on pilot projects, hopes to provide data on brushing habits and how they link to dental health and overall health.
Image Sourced via Flickr: Creative Tools
Featured Articles
NTT and medical technology company Olympus put on a demonstration, showing the IOWN APN's low-latency capability, for the first cloud endoscopy system
Richter BioLogics GmbH & Co KG's a new biopharmaceutical GMP facility in Germany will boost production capabilities and local employment
A pilot study from GE Healthcare has shown the value of Portrait Mobile Continuous Monitoring Solution, a leap in post-surgical monitoring efficiency