Pharma manufacturers need to adopt Industry 4.0 strategies
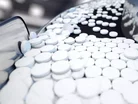
Over the past decade, many of the key ideas behind Industry 4.0, a.k.a. smart manufacturing, have been percolating throughout the economy and picking up momentum. The makers of foods, beverages, metals, electronics, and defence products have been taking the lead. In essence, Industry 4.0 replaces the traditional shop floor, characterised by discrete machinery and manual process controls, with a fully-digitised, highly automated, integrated manufacturing environment largely running their production.
At least in principle, a whole series of advantages can flow from making the transition to smart manufacturing. They include increased agility, greater efficiency, and higher quality production – each of which would benefit any industry.
But the $1.25 trillion pharmaceutical industry, for whom product quality means everything, has largely lagged behind. While there are important differences between making a life-saving medication and making a box of cereal for children, there is even more that they have in common.
Supply chain oversight
For example, both typically involve feed lines, granulation, blending, drying, heating, cooling, milling, sorting, compressing, coating, and product packaging – factory operations using machines that require constant monitoring and maintenance. And both need to be FDA compliant. But even more important is that they share a dependence on external supply chains whose raw materials, after processing, become integral to the finished product.
Having a clear picture of a company’s tier one suppliers as well as any second or third tier suppliers throughout their critical ingredients’ chain of custody, can help to identify flaws in those materials before they get baked into the finished product.
In the field of medications, that sort of problem occurred frequently until the late 20th century, as well as in third-world countries where regulations are typically more relaxed. But they can and do happen in the developed world too.
For example, in 2008, the blood thinner Heparin was recalled by the FDA due to contamination of its raw materials imported from China. Nearly 80 people in the United States had died as a result. Between 2012 and 2018, generic versions of an entire class of blood pressure medications were made in huge volumes using contaminated ingredients later found to have caused cancer. And there have been other instances as well, many of them resulting in massive fines and costly settlements. But they don’t have to happen.
Improving visibility along the supply chain is an integral part of the smart manufacturing concept. You can’t manage what you can’t see, and neither can your machinery. But keeping a digital ledger of materials can help to track the movements and the transformations of material procured from suppliers. That ledger can provide insights that lead to improved yields, higher quality, better safety, and consistent compliance by offering data-centric views of material flows throughout the product’s lifecycle.
Achieving digital maturity
Using cloud technologies to integrate internal data with external data sources – which is part of the Industry 4.0 vision – allows for real-time monitoring, prediction, response, and control all along the value chain.
Of course, elements of that capability are already in place at many factories. However, the key difference between what a smart manufacturing facility is capable of and what the earlier generation of plant technologies can do, is that Industry 4.0 involves taking the company’s current computing and communications systems and carrying them a step forward, where they interface with a new generation of autonomous digital devices and software. It does not necessarily involve a wholesale replacement of manufacturing equipment; rather, it focuses on improving how they’re controlled.
That’s not a simple matter; it’s a journey of learning and maturation which typically requires time. While it begins with simple data captured from a manufacturing process, it goes onto to the conversion of that data into information through analysis, and from there to knowledge resulting from the addition of context, sometimes through the use of artificial intelligence, and finally to actionable wisdom that informs the facility’s autonomous systems and cyber-physical machinery to make judgements, decisions, movements, and adaptations without human intervention.
It doesn’t all happen at once, and making that transition requires more than just adding new digital technology. Doing it successfully frequently involves creating new business models, negotiating new workforce arrangements, and mastering new leadership skills. In addition, there’s a risk that the transition can produce what some have called a “hidden factory” – one resulting from an unpredictable mix of old and new technologies which can lead to defective products and late deliveries.
The regulatory burden
Operating in a regulatory framework, as the pharmaceutical industry does, can be a serious challenge to introducing new technologies. As the authors of a thoughtful article in the International Journal of Pharmaceutics point out, the lack of regulatory precedent can lead the industry to retain conventional processes even when new processes, over time, can reduce the overall regulatory burden and increase product quality. Beyond that, there’s the challenge of filing regulatory applications in different countries with different rules and requirements.
However, there’s also some good news. For more than a decade, the FDA has been moving toward increasingly performance-based regulation. That form of regulation is based on measured outcomes rather than prescriptive processes, techniques, or procedures. In many respects, it is a great fit for Industry 4.0 which already uses extensive data and analysis to identify product attributes in the light of acceptance criteria.
Of course, adopting the advanced technologies and supervisory approaches needed to implement Industry 4.0 will not happen overnight. But it brings along with it the potential for higher output, increased safety, enhanced quality, improved cost savings, greater agility, and reduced waste – outcomes which other segments of the economy are now starting to enjoy and which the pharmaceutical industry is positioned to benefit from as well.
- AstraZeneca Sees Surge in Growth Amid Challenges in ChinaMedical Devices & Pharma
- CTP Builds Distribution Centre for Redcare PharmacyMedical Devices & Pharma
- Movianto’s Active Frozen Transport for Vaccine CampaignsMedical Devices & Pharma
- Kinaxis: Pharma Seeing Euro-wide Supply Chain ChallengesProcurement & Supply Chain